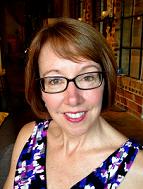
Q: What are of the few most common areas of waste found in a surgery center?
Elizabeth Toony: I am currently working on a Lean Six Sigma initiative that hones in on minimizing waste, improving quality and increasing cost savings. There are several strong issues to focus on.
Inventory is one of the biggest issues. In nearly all of the ASCs I have seen, overstocking is a problem. I am a nurse first; I appreciate that you don't want to be caught unprepared, but surgery centers do not need a month's worth of inventory sitting on the shelf.
Extra processing is another top area to focus on. Excessive paper work and repetitive tasks can eat up a large amount of time.
Overproduction plagues many ASCs. Everyone thinks more is better. It is not uncommon that everyone will ask for extra. Nurses may prepare extra medication before entering the OR for a case, but if it isn't used it has been totally wasted. Drugs are not cheap. Propofol isn't easy to get. Don't be drawing it up unless you will definitely be using it.
Motion, specifically related to supply storage areas, presents another issue that can lead to wasted time. The layout and organization of a facility is vital. When you go through the process of a spring cleaning, place the materials and equipment that are regularly used within easy reach. Place less high-traffic items out of the way.
Waiting is primarily an issue for patients, but it is entirely unnecessary for patients to come in two hours before their procedure. From the patient's perspective, it will seem like the surgery center does not consider their time valuable.
Human potential is something ASC leaders might not necessarily think of when considering waste, but if you aren't utilizing your people's resources to the fullest potential, you are wasting them.
Q: Where can administrators cut down on inventory?
ET: Purchase items on consignment, especially implantable items. You still have to store them, but there is no longer a big chunk of cash sitting on the shelf. Another way would be to begin ordering supplies twice a week. If you order in bulk once a week, you will always have buildup. Most ASCs work with a manual inventory process. Take advantage of the time this takes and assess your inventory. What hasn't moved? It takes time, but you can accomplish a thorough spring cleaning each time you do inventory.
Motion also plays into your spring cleaning. Organizing your inventory shouldn't be a constant process. This would lead to chaos and no one would know where things are located. Instead, make inventory a periodic, two-day process. Hold a few meetings leading up to those two days. Set goals. Then, during the process check for waste. Count your stock and organize everything based on how often it is used.
Q: What can be done to eliminate time wasted through extra processing and over production?
ET: Eliminating extra processing is simply a matter of putting better processes in place. Combine tasks where it makes sense and eliminate unnecessary paperwork.
If you know you have problems with overproduction, take the time to look for the biggest problem areas. Recruit a few staff members to keep an eye out. Nurses can be drawing up unnecessary drugs; drugs are definitely a big area. The business office can be taking two sheets of labels when one would suffice.
Physician preference cards can be a source of over production. Nurses may pull every single supply on the card and put these in a bin for the surgeon. Everything will be opened, whether or not it is used. Instead, have the supplies nearby if they are needed, but don't have them opened unless requested. Mark the items on the card that may not be needed. Identify the problem and put in place new protocols to solve the matter.
Q: How can administrators work with physicians to reduce time and materials waste?
ET: Physicians function very much in the here and now. They aren't thinking about the bigger picture. As an administrator, you should bring the bigger trends to their attention. Cue them into how much supplies cost. Physicians should realize if they are casually throwing away an unused $60 item. Ask them to consider updated preference cards. Show physicians how their case costs stack up against one another.
Physicians want to do as many cases as possible, but if they arrive late for cases time is wasted. It starts a domino effect that puts everything behind schedule. In my center, I keep a report card of late arrivals. It helps that physicians can see prompt arrival can even allow for more cases to be done.
Q: What processes can be put in place to reduce patient wait time?
ET: Consider using a patient portal. Patients can fill out a great deal of information ahead of time, all without taking up time. They can come in an hour before their procedure, instead of two hours before. Not all surgery centers have a patient portal, but always look for ways to combine patient documents and get rid of the unnecessary ones.
Q: What can administrators do to promote staff commitment to waste reduction?
ET: Administrators should have a relationship with each staff member. Take the extra effort to support them and find areas where they could grow. If a staff member has an analytical personality, you've found a great fit for the quality team. Play to your staff's strengths. If administrators cut staff members loose after training and never look back, they are missing an opportunity to utilize their staff's potential to the fullest.
More Articles on ASC Efficiency:
10 Key Items for Great ASC Administrators to Focus On
6 Things to Know About Controlling ASC Labor Costs
4 Methods to Reorganize ASCs for Success